Peiseler offers various modular retrofit solutions under the ATC series. These NC subdevices boast a cutting-edge design and a competitive price. During development, we focused on optimising the drive train, harmonising the sizes and using the same design principles across all components. We are continually expanding the range of models in the ATC series.
Find out more about the technology behind our modular product range
Discover the concept, the technology and benefits of our standardized solutions.
Peiseler retrofit solution series
Drive variants in detail
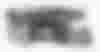
Worm gear drives
Peiseler uses three-piece worm gears, a well-known design developed by Ott. These gears consist of a worm wheel and a two-piece worm, the shank worm and hollow worm. During assembly, we adjust the gear so it is backlash-free. Readjusting the worm during its service life is simple with a commercially available mounting tool. The design advantages are a compact gear ratio, high mechanical precision and the control's excellent regulatory quality. Heat limits the duty cycle.
The benefits for you
Simple commissioning/easy installation
Easily adjustable worm gear
Maximum drive moment and low backlash
Self-braking (safety feature)
Cost-effective solution for positioning applications
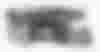
Components in detail
Rotary manifolds
We build rotary manifolds for air, water, cooling lubricant or oil up to 250 bar pressure. We have developed low-friction seals in rotary manifolds to meet the demands of the mould-forming industry and high-speed axis applications. We work with our suppliers to develop special lines of seals with an optimum sealing performance. Coated manifold shafts withstand the loads of the dynamic, continuous movements common in free-form surface production.
The benefits for you
Developed in house/maximum design flexibility
Can be adapted to suit any requirements
Nested design available
Maximum availability/process reliability
Low-maintenance
Compatible with a wide range of media
All core assemblies from a single source!
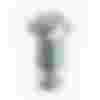
Passive clamp
Our highly responsive, patented axial clamp is designed for low distortion. The clamp – which activates with a pressure of 60 bar and is open when de-energised – reduces the span-to-span time. Thanks to its design and targeted force flow, the clamp increases the rigidity and damping capacity of the subdevice, which in turn promotes a longer tool life and protects the surface of the workpieces. The material combination is designed to ensure a long service life, minimise maintenance costs and reduce downtime.
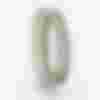
Pneumatic clamp
All machine tools provide access to the pneumatic systems. Thanks to our specially developed operating principle, our pneumatic clamps boast friction torques that are virtually identical to those of hydraulic clamps.
Subdevices with 6 bar pneumatic clamping can be used in any application with a compressed air supply, making them the number-one choice for customers looking for an easy and clean retrofit solution.

Hydraulic clamp
Our highly responsive, patented axial active clamp is spring-preloaded and is ideal for use as a safety clamp in horizontal axis configurations. The material combination is designed to ensure a long service life, minimise maintenance costs and reduce downtime.
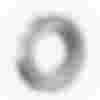
Available sizes
All Peiseler subdevices are designed for a wide range of applications. From workpiece positioning and machining of the smallest components, to handling heavy loads and outsize workpieces, Peiseler offers the optimum solution, with seamless scaling to suit your requirements. We can also adapt our subdevices to meet your individual needs.
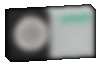
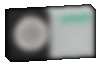
Minimum
|
Maximum
|
|
|
140 mm | 450 mm |
|
120 kg | 1.800 kg |
Application examples
Series-produced core components
Optional modifications
The best for your machines
Modularity – Our housing features a modular design, enabling you to position the drive motors on the left or the right of each coupling depending on the space available, with the option to add an adapter drive – making our devices even more flexible.
Reliability – All key components are checked at multiple stations during the production process, with functional tests completed on every component before delivery. This process ensures high reliability and a low returns rate, saving you time and money.
Rigidity – Spacious, FEM-optimised housing structures provide exactly the right levels of rigidity and damping for your process – so you can achieve an even better cut and surface quality.
Simplicity – Our installation-ready devices come adapted to your machine interface, making assembly easier and saving you time.
Durability – Opting for low-maintenance, high-quality components reduces maintenance and servicing costs and ensures high machine availability for longer.
Maintenance-friendly – Our new axial threaded bushes, combined with our axial shoulder bearings, allow drives to be maintained and serviced in the field. The worm shaft can be easily adjusted without grinding or other adaptations, significantly reducing maintenance and servicing costs.
Power density – A high power density is the most important design criterion for our ATC series. All of the drive train components have been overhauled and optimised for low weight to boost the dynamic performance of the drive train. The new design also reduces installation space requirements.
Accessibility – During the design process, we've focused on making our devices easy to assemble, with good access to components – reducing repair costs in the event of damage.
Robustness – Peiseler's hydraulic and pneumatic clamps are replaceable, with high holding torques and fast response times. Our carefully selected materials reduce susceptibility to corrosion and prevent fretting even in extreme conditions. This results in high torques and a long service life – as well as contributing to high machine availability.