Peiseler-Rundtakttische sind das Zentrum einer rotativen Rundtaktmaschine mit diversen Stationen zur Bearbeitung, sowie einer Be- und Entladestation. Eine besondere Anforderung an unsere Konstruktion ist dabei das Erreichen einer maximalen Leistungsdichte für hochdynamische Taktzeiten auf kleinstmöglichem Bauraum.
Bislang größte Multi-Achskombination in 200-jähriger Historie sorgt für Steigerung der Produktivität von Leichtbaukomponenten
Remscheid, 4. Februar 2021 – Mit einem Rundtakttisch trägt Peiseler zur Produktivitätssteigerung eines namhaften deutschen Automobilherstellers bei. Die Innovation hat das Remscheider Unternehmen mit seinen Kunden UNIOR Werkzeugmaschinen in Slowenien entwickelt. Der Rundtakttisch ist gewissermaßen das Herzstück einer dort hergestellten Werkzeugmaschine, mit der schließlich Leichtbaukomponenten für die Herstellung von Elektroautos bearbeitet werden. „Er hat einen Durchmesser von 3.000 Millimetern und wiegt zehn Tonnen“, erläutert Marc Gronau, Vertriebsleiter bei Peiseler, „und ist damit die größte und anspruchsvollste Einheit dieser Bauart, die wir jemals in unserer 200-jährigen Unternehmensgeschichte gebaut haben.“
Basis ist der schneckenradgetriebene Peiseler-Drehtisch ATU 1600, der mit einem direkten Wegmesssystem sechs Zweiachs- Schwenkeinrichtungen vom Typ ZATC 300 in fünf Schritten von einer Bearbeitungsstation zur nächsten und danach mit einem Pilgerschritt in die Ausgangsposition taktet. Insofern verfügt der Rundtakttisch über insgesamt 13 Achsen sowie eine maximale Zuladung von 250 Kilogramm je Station. Sie gewährleisten eine hochpräzise Simultanbearbeitung der Werkstücke.
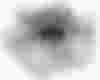
Basistisch: Konfigurierbares Antriebskonzept
Präzisionsmaschinenbau
Der Peiseler-Rundtakttisch ist das Zentrum der gesamten Rundtaktmaschine mit fünf Stationen zur Bohr- und Fräsbearbeitung sowie einer Be- und Entladestation. „Eine besondere Anforderung an unsere Konstruktion war dabei nicht nur das Erreichen einer maximalen Leistungsdichte für hochdynamische Taktzeiten auf kleinstmöglichem Bauraum“, betont Gronau. „Um die stets vorhandenen Toleranzen möglichst gering zu halten, galt es, jede einzelne der Zweiachs- Schwenkeinrichtungen auch untereinander in höchstem Maße exakt zu positionieren.“ Eine weitere komplexe Aufgabe sei die Medienversorgung zum Spannen, Lösen und Überwachen der Werkstückspannvorrichtung gewesen. Dafür setze man einen Drehverteiler mit acht Kanälen ein.
„Insofern haben wir nicht nur den bislang größten Rundtakttisch gebaut, sondern auch eine kundenspezifische Lösung entwickelt, die in der Produktion von Elektrofahrzeug-Komponenten für kurze Taktzeiten und niedrige Stückkosten sorgt“, freut sich Gronau. Dank der hohen Präzision habe Peiseler als Hersteller von Wendern, Drehtischen, Zweiachs-Schwenkeinrichtungen, Schwenkköpfen und Werkzeugwechseltischen auch einen Anteil an der prozesssicheren Fertigung von zukunftsorientierter Mobilität.
Kernkomponente: 2-Achs-Schwenkeinrichtung
Verwendete Baureihe(n)